The biggest fear of any aquatic facility manager is a pool shutdown. Unfortunate events such as a fecal incident are impossible to control; however, a pump or filter should never be the cause of a facility closure. There are, in fact, several best practices one can follow to avoid some of the most common causes of pump and filter failure. The following guidelines, which have been developed in the field over many years, should be included in any aquatic facility maintenance plan. From daily checks to keeping specific spare parts on hand, aquatic facility managers can avoid a pump or filter failure from causing an aquatic facility to shut down.
Pump failure
It is important to remember all of the reasons that could cause a pool pump to fail. In many cases, there are simple recommendations that can be followed to ensure pumps do not stop operating.
Pump runs dry
It may seem obvious, but one of the main reasons for a pump to fail is because it has been allowed to run dry. When this happens, it could cause a loss of pressure, which can result in damage to the casing, impeller, and seal. When the seal fails the pump will seize, bringing it to a halt. This is not the case for all situations, however, as some pumps will run but the faulty seal will cause the unit to leak.
One of the most common reasons for a pump to run dry is because it has been improperly sized, resulting in cavitation. This means the pump is too large for the pool application. For example, a 283,905-L (75,000-gal) pool running 787 liters per minute (lpm) (208 gallons per minute [gpm]), can be handled by a 5-hp pump. However, a pool of this size is often equipped with a 7.5-hp pump, which is not using the valves or a variable frequency drive (VFD) to bring the flow rate to the proper level.
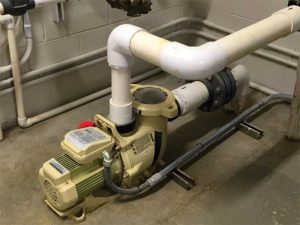
The best way to avoid a failure caused by improper pump sizing is to install a variable frequency drive (VFD) that is capable of bringing the flowrate up to where it needs to be to prevent the pump from running dry.
A consequence of over-sizing the pump will more than likely result in cavitation or possibly even seeing the unit run dry and fail. The best way to avoid a failure caused by improper pump sizing is to install a VFD that is capable of bringing the flowrate up to where it needs to be to prevent the pump from running dry.
The same thing can happen if the pump has an air leak, if the pump’s strainer basket is full, and/or has not been cleaned out properly. That said, the pump’s strainer basket should be visually inspected at least once a week. Dirty strainer baskets reduce filter and heater efficiency and put abnormal stress on the pump motor. In addition, sometimes, if the valve on the suction side of the plumbing is closed off, it can also cause the pump to run dry and shutdown.
Similarly, a pump can run dry as a result of a loss of prime. Essentially, this means the pump does not have enough water coming into the suction side and, as a result, it does not work properly because it will not prime. When troubleshooting this problem, check the suction piping and valve on any suction gate valves for any issues. The lid on the pump strainer pot should also be secured, while at the same time making sure the lid gasket is in place.
It is also important to check the pool’s water level to make sure the skimmer is not drawing air. The suction lines, pump strainer, and pump volute (the casing that receives the fluid being pumped by the impeller, slowing down the fluid’s rate of flow) must be full of water. The valve on the suction line must also be working and open (some systems do not have valves).
Pump runs backwards
This may sound ridiculous, but it is quite common for pumps to fail when they ‘run backwards.’ For some technicians, it is not unusual to receive a call from the field with a report that a pump is not, in fact, pumping the proper amount of water, resulting in the motor running hot and at higher amperage.
These symptoms could point to the fact the motor is ‘wired backwards.’ Essentially, the wiring of the pump is such that the motor is not rotating in the proper direction that it is designed, which not only affects the rotation of the impeller but also the flow of water through the pump.
Pump damage from improper water chemistry
Improper water chemistry can also lead to pump failure. Often, when the pool’s water chemistry has a low pH, the bronze cast impeller within the pump motor can begin to deteriorate from corrosion.
Anytime water chemistry is not balanced, especially for a prolonged period, pool pumps suffer the effects of corrosion. When chlorine levels reach between 1 and 3 parts per million (ppm) and the pH reaches between 7.2 and 7.6, there is a high probability corrosion will affect the life of the pump. It will also affect the flow rate, as the water coming out of the pump will be reduced.
In addition to corrosion, pump impellers can fail as a result of cavitation, which means the pump is pushing or trying to push, much more water than what it was designed to do. If the failure is cavitation, the pump will start to make a loud rattling sound when the impeller is deteriorating.
To avoid deterioration of the bronze impeller, it is important to keep pool water chemistry properly balanced, keeping a particularly close eye on chlorine and pH levels. The best way to do this is to use an automatic chemical controller. If an automatic controller is not present, daily testing of the water can also help to protect against imbalanced water chemistry.
In addition, when dealing with non-plastic pumps, or those with bronze impellers, aquatic facilities should keep an extra impeller on-site for quick replacement. As a best practice, aquatic facilities should also have an extra motor on hand to avoid having to shut down the pool.
Inadequate voltage to the pump
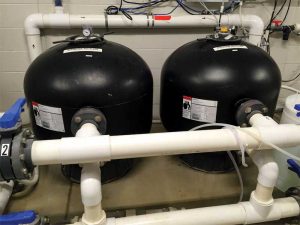
When there are multiple filters installed on a pool, it is important to ensure the plumbing is balanced so water goes through each filter equally.
When the power (voltage) running to the pump is too low or too high, it can cause undue strain on the pump, resulting in premature failure. To avoid this from happening, it is important to test the power going into the pump at the source. If the voltage is too low/high or is inconsistent, consider adding a VFD, as it will regulate the power going into the pump.
Pool pumps with induction motors, which only operate at one or two speeds, tend to draw more energy than is required to circulate pool water. These units must constantly operate at high speed to perform the pump’s most demanding jobs (e.g.running a waterfall or pool cleaner). However, it takes far less power to simply keep the pool water filtered— a difference single-speed pumps cannot address.
In some cases, a variable-speed pump (VSP) offers the ability to be programmed to operate at set speeds to deliver the proper flow rate for each task it performs. This enables an aquatic facility to reduce energy consumption, which may also solve the problem of incorrect voltage to the pump.
VSPs can also be programmed to achieve turnover times of exactly six hours, even if the filter is dirty. This allows motor speed, power, and energy to be reduced during times when the filter is clean, instead of sizing the pump to assume worst-case operating conditions.
Wrong pump for the application
Sometimes, a facility’s auxiliary features (e.g. spray pads, fountains, and waterfalls) should also be considered, as it is common for them to use the pool’s main pump. These auxiliary features could be causing excessive strain on the equipment.
To avoid undue stress on the pool pump, a separate pump may need to be added for each auxiliary load. To determine if the pool pump is under too much strain, take the time to evaluate the following:
- Determine the flow rate in lpm (gpm).
- Calculate total dynamic head (TDH) (which is the pressure head difference between the inlet and outlet of the pump) to account for friction loss. Adding 6 m (20 ft)/TDH for a dirty filter is optional.
- Refer to the pump’s performance curve to select the preferred unit.
- Locate the pump horsepower that is required by plotting lpm (gpm) versus TDH. If the plotted point falls between two pump sizes, it is best to select a larger pump size.
- Verify the selected filter can handle the system’s flow rate and be sure the minimum backwash flowrates can be achieved.
It is also important to be sure the pump on the pool matches its filters. For example, a 7.5-hp pump should not be installed on a pool with filters that cannot handle that pump’s flow rate. If the pump needs to flow 1135 lpm (300 gpm), one must ensure the filters that are installed are not only capable of handling that flow, but also at the required filtration rate (usually 611 lpm/m2 [15 gpm/sf]). Further, a 2-hp pump should not be used on a pool that requires a 3-hp (or more) unit to keep up with the turnover rates. Just because a particular pump is on a pool, does not mean it is the right one for the job.
Motors flooding out
Although the industry has mainly switched to pumps with totally enclosed fan-cooled (TEFC) motors, in which the motors are sealed and protected from potential flooding, there are still thousands of pump motors on pools in Canada and the U.S. that are open drip proof (ODP). Unfortunately, if water gets inside the motor, it can damage the internal components. Equipment rooms with ODP pumps that experience flooding (e.g. from weather), are potential targets for equipment failure. Changing the pump to a newer TEFC pump will eliminate this potential problem, or make sure the motor is protected as much as possible from potential flooding.
Other causes of pump failure
Any aquatic facility maintenance plan should always include an extensive checklist around the heart of the equipment room, especially for the pumps. Pump baskets that are not cleaned out, lack of ventilation, and motor bearings that are not greased on a regular basis can all lead to pump failure. That said, motor bearings should be greased, if required, at least once a year, but preferably every six to nine months.
Filter failure
Similar to pumps, filters need to be maintained at all times to protect against failure. To accomplish this, a very specific checklist is essential to prevent a filter failure and a potential aquatic facility shutdown.
Too much water
It is not always considered, but too much water going through the filters can actually damage the internal components. To check the flow rate, a flow meter should be installed before the filters to show the amount of water that is going directly into the unit. By doing so, aquatic facility managers can adjust (as needed) the amount of water flowing into the filters. The best way to slow the flow of water is to slow down the pump. This can be accomplished by using a VFD or by slightly closing off the valves.
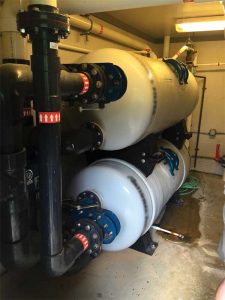
It is not always considered, but too much water going through the filters can actually damage the internal components.
In addition, excessive water flow through the filters also limits the equipment’s ability to filter the water efficiently, which could potentially result in a facility shutdown.
Filters are undersized for the application
When there are multiple filters installed on a pool, it is important to ensure the plumbing is balanced so water goes through each filter equally. If the plumbing is not balanced, the filter(s) that are being unnecessarily stressed, will likely fail. For example, if an aquatic facility has a pool with 378,541 L (100,000 gal) of water and a six-hour turnover rate, this would be equivalent to a flow rate of 1052 lpm (278 gpm).
If there were two filters installed, each one specified to handle 530 lpm (140 gpm), then in total, the filtration system could technically handle a flow rate of 1060 lpm (280 gpm). However, in reality, the pool would come up short with these two filtration tanks if they are to comply with the rule of 56.7 lpm (15 gpm) per square foot required on commercial pools. In this example, a third filtration tank that can handle 530 lpm (140 gpm) would be required to meet the needs of this application.
Damaged or missing laterals in sand filters
Unfortunately, if facility managers are not careful when loading the sand and gravel into a filter, the laterals can be damaged fairly easily (causing cracks), which can result in filter failure. In fact, most manufacturers recommend filling the filter with some water before adding the sand—and especially before adding gravel—to help protect the laterals.
Occasionally, newly manufactured sand filters can be inadvertently missing a lateral. In addition, when laterals are replaced, sometimes one can be forgotten. Therefore, it is important to inspect filters carefully to be sure all laterals are present, as well as to ensure they are secured in place properly to avoid them from becoming loose and, in a sense, be missing from the hub.
If an aquatic facility manager sees sand entering the pool through the return lines, it is most likely a problem with the laterals. The best way to resolve this type of issue is to empty the sand and gravel from the filter and inspect all of the laterals, as well as the hub, and replace any parts as needed.
Improper mixture of sand/gravel
Most manufacturers have a table available that shows how much pea gravel and sand should be placed into a sand filter. If there is too much sand and/or gravel, it can affect the filtration process, as well as cause the filtration system to fail. If the mixture is imbalanced, it is best to refer to the filter manual. In doing so, this may require the mixture to be replaced completely.
A maintenance program is important
All aquatic facilities should establish a comprehensive maintenance program for the equipment room, which must include a specific action plan for the pumps and filtration systems used on pools and other water features. Avoiding a pump and/or filtration system failure is the first defense against an aquatic facility shutdown.
This article was written by Mike Fowler and originally appeared on Pool & Spa Marketing [link].