A child drinks 44 mL (1.4 oz) of water every hour they play in a pool; therefore, it is crucial to ensure the water is clean. One major component to the cleanliness of pool and/or hot tub water is the filter. Today, one of the most popular media used to cleanse water are filter cartridges, which are typically made with polyester spun bond non-woven filtration fabrics. This media is pleated into many folds, seamed, and formed into a cylinder with a plastic core for support against incoming water flow and urethane end caps, bonded onto the ends. The polyester fibers used for this purpose can vary based on size and shape. Industry-wide, filter manufacturers use a fabric weight of 135 g/m2 (4 osy) for pool cartridges and 100 to 110 g/m2 (3 to 3.2 osy) for hot tub filters.
The shape of things to come
Spunbonded fabrics are made with pelletized raw material such as polyester, which is melted, extruded and drawn into many small endless fibers. These fibers are ejected from spinnerets, which as the word intonates ‘spins’ these endless fibers onto a fast moving belt. Spinning helps in making the web uniform across its width in what would be an otherwise uneven process. The resulting tangled web of fibers creates a permeable sheet, which contains openings of varying size called pores. These pores are responsible for trapping debris on the surface of the fabric and, at the same time, allow water to pass through.
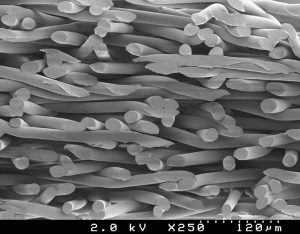
Round filter fibre
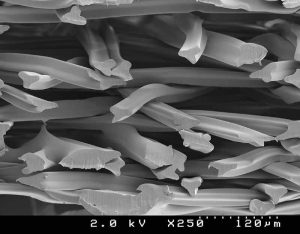
Tri-lobal filter fibre
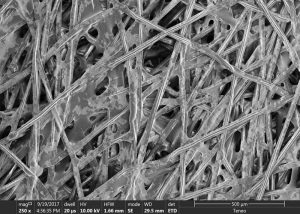
Filter fibers coated with clarifier
During the extrusion process, there is a possibility to form the shape of the fiber along its cross-section. In the pool and hot tub industry, there are two predominant filter fiber shapes—round and tri-lobal. Because of their shape, tri-lobal fibers are claimed to offer a more torturous path for debris to travel through. This gives the web a better chance to capture whatever debris is passing through it. Round fibers can outperform (in terms of filtration) tri-lobal fibers if they are made from finer fibers. Due to their smaller diameter, round fibers will have more surface area compared to tri-lobal counterparts of a larger diameter of the same unit weight. More fibers per given weight produce more pores, which offer more fiber crossover points, and ultimately provide finer porosity.
At the final stage of the creation of the fabric, fibers need to be bonded together so they create a rolled good allowing for subsequent processing by cartridge manufacturers. Based on the type of fiber used, bonding can be achieved or enhanced, using one of the following methods.
Needle punch
Fabric fibers are entangled and mechanically interlocked by punching the web with a series of barbed needles. This provides strength to the fabric along its thickness.
Hydro entanglement
Similar to needle punching, this bonding method uses high-velocity water jets to entangle and mechanically interlock the fabric fibers along its thickness.
Thermal bonding
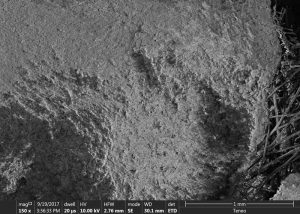
Under microscope, calcium deposits blind the surface of the filter fibres
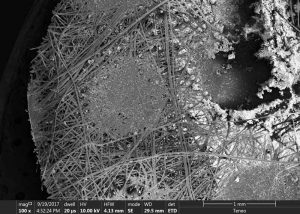
Fine algae particles embedded in the depth of the filter fibres
- Calendaring or embossing—The heated web is squeezed between two rolls (smooth or patterned) which force intimate contact of the molten fibers with other fibers in the web. Often the calendar rolls are heated; if the rolls are smooth, the web is uniformly bonded. If the rolls are patterned, an embossed web results typically seen as a very even pattern of small points across the web.
- Air bonding—The web is thermally bonded by passing it through an air dryer or heater. The result is a bulkier and loftier media.
- Ultrasonic bonding—This is a relatively new technology that uses high-intensity energy to melt and form bonds from thermoplastic fibers.
- Hot melt bonding—The hot melt thermoplastic is extruded onto the web and, while still in the molten stage, it penetrates and bonds the web.
- Chemical bonding—A chemical binder agent or resin is used to bond the web.
The mechanics of a cartridge filter
Cartridge filters rely on the surface area of the filtration fabric, unlike a traditional sand-type filter, which relies on the diameter of the tank, as well as the depth of the sand bed. As water passes over a cartridge filter, it starts building a layer of dirt and debris on its surface, which is commonly referred to as filter cake. Over time, the filter cake continues to accumulate on the surface of the cartridge trapping smaller and smaller debris.
As the filter loads, the throughput (flow) of the system begins to diminish, resulting in an increase in pressure on the filter system. Field service technicians and end users monitor a pressure gauge on the filter tank to judge how far along the cleaning cycle is.
Drawing upon the different ways to manipulate a fabric during its formation, certain characteristics can be tweaked to improve the performance of a cartridge filter without creating a dramatic spike in the system’s operating pressure. Again, by reducing the diameter of a fiber, it can increase the number of fibers in a fabric. Smaller fibers offer more cross-over points, which creates finer pores in the fabric. Filter cake then begins to form on the fabric sooner. As mentioned, all polyester media must be bonded to ensure the fibers stay together. Through observation, a uniform bonding pattern also encourages the formation of a filter cake more so than randomly bonded fabrics. This has a positive impact on the cartridge’s dirt holding capacity, as the debris is more evenly distributed.
Regardless, there will always be smaller particles that become trapped in the depth of the fabric’s web and cannot be released from the filter, even after washing the cartridge. As the cartridge continues to provide service, a shorter operational cycle can be expected between washes than when the cartridge was originally installed.
These seasoned cartridges offer the benefit of finer filtration, albeit in shorter periods of use. Some service technicians prefer to use these older filters when vacuuming dead algae (smaller than 4 microns) from the pool or at the start of the pool season.
When is it time to clean the filter?
The industry rule of thumb is to clean/service the cartridge filter element after the system pressure increases by 8 psi; however, the U.S. Center for Disease Control (CDC) states: “A typical-use pool should have a pump and filtration system capable of pumping the entire contents of the pool through the filters every six hours.” This is generally interpreted as four turnovers per day to ensure the pool does not become cloudy or experience other water quality problems.
To maintain filter cleanliness, there has been a growing trend in the number of homeowners who use flow meters on their pools as a standard to determine when their filter needs to be cleaned. In some cases, an increase in pressure by 10 psi would still ensure four turnovers a day and a trouble-free pool; however, in some instances, an increase in pressure by 4 psi could result in less than four turnovers a day and a cloudy, problematic pool situation. This could always be balanced by plumbing modification and sizing the pool equipment correctly.
How to clean a cartridge filter
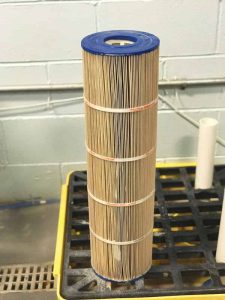
As the cartridge continues to provide service, a shorter operational cycle can be expected between washes than when the cartridge was originally installed
It is a good idea to refrain from using a strong acid to clean a filter, as they can bleach out the product to look as though they are as good as new. However, a strong acid can negatively influence the fibers and, as a result, the filtration performance. It is also recognized that certain treatments and chemicals added to the pool may have non-reversible impact on the filter and may shorten the life of a filter.
The field experiment
With help from Rich Tarricone of Aquatic Pool Systems in Florida, the 2010 Perfect Pool Guy winner, the authors were able to conduct a brief study on filters used in pools located in Florida. It looked at how certain pool conditions, and the chemicals used in the treatment of that condition, affected the filter fabric at a microscopic level.
The images showcase what happens to a cartridge filter under different conditions, including:
- Using clarifiers to increase filter efficiency by capturing finer particles.
Clarifiers are used to increase the filtration efficiency; however, they can become difficult to clean, resulting in reduced life of the filter.
A gel-like substance is formed and, over time, led by debris from the pool, it adheres to the fibers. - Using phosphate removers to reduce phosphate levels in pools.
- Using algaecides to treat algae infected pools.
Algae blooms are difficult to treat. The algae fines could be as small as sub-4 microns, which may become trapped in the web of the filter cartridge, and would require a thorough cleaning. It is always recommended to use an older set of filters. - Vacation home/commercial filters, which see many bodily fluids/oils.
Oil and dirt bind over filtration fabric, forming a film, which reduces the filter’s dirt holding capacity and performance lifespan. This mixture is difficult to clean and often requires degreasing chemicals to help remove the oil from the fabric’s surface. - Calcium scaling.
Calcium deposits are difficult to clean from the surface of the filter. It compromises the effective surface area of the filter and its ability to hold debris.
In conclusion
Under normal conditions, cleaning a cartridge filter using a simple garden hose is sufficient to remove a large portion of the filter cake. When using mechanical agitation such as a brush to clean debris, it is important to use care to minimize any damage to the fabric web.
For heavier soils and other conditions where specialty chemicals and filter aids were used, these treatments may affect the service of a filter; therefore, it is important the recommended cartridge cleaning instructions are followed to prevent the calcification of debris on the fabric surface.
This article was written by Richard Medina and Abhi Pillai and originally appeared on Pool & Spa Marketing [link].