Energy efficient heating systems are here to stay. Condensing boiler units as well as geothermal and solar thermal heating systems can produce considerable savings in their operation. However, they may not operate at maximum efficiency if the systems they serve are not designed to use less energy. As a designer, one must consider any limiting steps that could impede a system from operating at peak efficiency.
Heat exchangers typically used in pool and spa heating are instrumental in transferring heat from the source (heating system) to the load (pool/spa). If they are not sized, designed or built to the proper specifications they will not make efficient use of the heating source, or worse yet, fail to satisfy the load demand.
There are several types of heat exchangers on the market, including:
- Shell and tube (Type 1):
- Spiral (Type 2); and
- Braised plate and plate and frame gasket (Type 3).
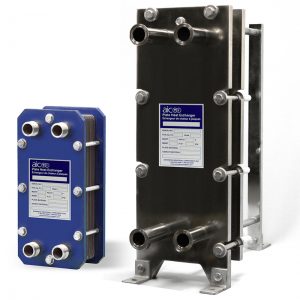
Framed plate heat exchangers are designed to be serviceable and configurable by having removable plates and gaskets.
When determining what design should be used on a particular project, especially if energy efficiency is crucial, it is important to look at the heat exchanger’s performance chart first to ensure the type selected is designed for efficient pool heating.
Performance matters
‘Type 1’ and ‘Type 2’ heat exchangers (listed above) historically have rapidly declining scales of efficiency as the entry water temperature drops. These heat exchangers are commonly applied to higher temperature applications and do not work well for high-efficiency, low-temperature applications such as geothermal, solar or condensing boiler systems.
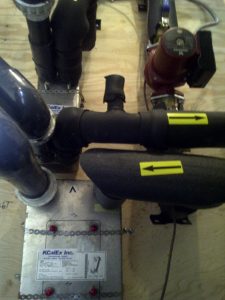
Type 3’ heat exchangers are better suited for low system entry water temperature (EWT) due to their design and larger surface area for heat transfer.
Type 3’ heat exchangers, however, are better suited for low system EWT due to their design and larger surface area for heat transfer. Increasing water flow (litres/gallons per minute [lpm/gpm]) or the number of plates in the system will cause the load leaving water temperature to be closer to the source EWT from geothermal, solar or boiler systems. This greatly increases efficiency by permitting the use of low EWT.
However, consideration should be given to the implications of the increased pressure that is required to pump larger volumes of water through more plates on a small heat exchanger. Therefore, careful pump selection is critical to success in this area.
Additional considerations
Ensure all wetted areas and connections are made of a material that is resistant to corrosion, which may result from the liquid (e.g. water, saltwater, chlorinated/brominated water or antifreeze) passing through the system. Other component materials in the system may contribute to corrosion effects by their reaction with the liquid stream.
Load sizing
Make sure the overall heat transfer is sufficient in providing heat quickly enough to satisfy the customer. For example, the system may have enough energy to maintain the heat in a spa/hot tub, however, if it takes several hours to heat the water, the customer may be unsatisfied.
How do they work?
The basic principle of a heat exchanger is to transfer heat when a temperature difference exists between two fluid flows. A simple formula used to evaluate heat exchange can be expressed in the following ways:
BTU = GPM X ΔT x 498
GPM = BTU / ΔT x 498
ΔT = BTU / GPM x 498
This formula helps to find different ways of satisfying the goal of ensuring enough heat is transferred to match the load. In this case, heat is measured in British thermal units (Btus). A Btu is the amount of energy required to raise the temperature of 0.45 kg (1 lb) of water by one degree, while the flow of liquid through the heat exchanger is measured in lpm/gpm. The constant ‘498’ represents the specific properties of water. If the liquid is changed to another medium, this constant also changes. Finally, ΔT is the temperature difference experienced by the water across the heat exchanger.
For example, if the load requires 100,000 Btus, the solution can be met in the following ways:
Water volume
One way to exchange heat is to increase the volume of liquid passing through the heat exchanger. For a specific Btu heat exchange, as the flow increases the temperature difference (ΔT) is reduced (e.g., to achieve a five-degree temperature difference an approximate flow rate of 151 lpm (40 gpm) would be required, while a 50-degree temperature difference would only require 15 lpm (4 gpm).
Temperature difference
Another way to exchange heat is to increase the temperature difference across the heat exchanger. For instance, by keeping the flow rate a constant the larger the temperature difference the more heat will be transferred (e.g., setting the flow rate at 38 lpm (10 gpm) the temperature difference required would be approximately 20 degrees).
Hotter temperature is not better
What about the effect of lowering EWT? Using the examples above, if the supply EWT came in at 82 C (180 F) and left at 71 C (160 F) it would achieve the same result as if the supply EWT came in at 48.8 C (120 F) and left at 37.7 C (100 F). Therefore, all things being equal, it seems as though EWT is not a factor; it appears to be all about the temperature difference.
However, EWT is a factor. In fact, hotter water is less efficient to produce as the heater’s chimney throws out hotter exhaust gases. When using energy efficient heating sources, it is all about the supply water temperature. The lower the temperature required to heat the load, the higher the rate of return on the source heating system. Therefore, designers should always look at their maximum or primary load temperature and see what can be done to bring that temperature lower. Lower heating system temperatures will reduce losses at the chimney, equipment and piping, and will provide a larger amount of heat that can be efficiently exchanged.
Not all heat exchangers are created equal
Geothermal implications
Geothermal operating temperature limits in hydronic applications are typically around 46 C (115 F). At higher temperatures most geothermal systems will not operate well, or will operate with a very poor coefficient of performance (COP) (the amount of heat required divided by the amount of energy used to do produce that heat). However, the low-operating temperature and ‘free energy’ heat source of geothermals permit the design of an extremely efficient heating system.
Boiler implications
Modern energy efficient condensing boilers achieve four things:
- Operate at a very high annual fuel utilization efficiency (AFUE) value;
- Modulate supply water temperature based on outdoor air temperature;
- Modulate gas usage based on system demands; and
- Extract energy from exhaust gases by cooling them to the point where moisture contained in the gases condense and release additional energy (‘latent’ energy at an approximate rate of 1,000 Btu/L[lb] of water).
Even though a boiler can produce 82 C (180 F) water, this should not be set as the system’s operating temperature. High-efficiency boilers are meant to condense. Condensing is a process in which the exhaust vapours in the combustion process change from gas to liquid. To achieve condensation, the return water temperature must be 54.4 C (130 F) or less. A good rule of thumb to follow is the lower the exhaust temperature, the more efficiently the system is operating. Designing the system to operate at 60 C (140 F) or less will typically allow the boiler to operate in the high-efficiency range.
Conclusion
Careful system and heat exchanger design is critical when making use of the latest low-temperature and low-energy cost heat sources that are available. Proper selection of the heat exchanger component is essential to providing long-term customer satisfaction.
This article was written by Steve Hamoen and originally appeared on Pool & Spa Marketing [link].