Pumps are the heart of a pool circulation system—not only are they the vehicle that moves water through the various systems, but also now the focus of substantial rebates which can drastically reduce the costs of owning and operating a pool. That said, it is important to get back to basics and understand the significance of hydraulics on residential and commercial pools and why utilities are pushing for consumers and aquatic facilities to install variable-speed pumps (VSPs). To take advantage of utility rebates, pool professionals need to understand how pumps work, what the difference is between single and variable-speed models and the factors that influence energy savings in the equipment room.
How centrifugal pumps work
All pool pumps are centrifugal. They have a shaft-driven impeller that rotates inside a casing, which allows water into the suction port (inlet) where it is then ‘thrown’ to the outside of the casing before exiting through the discharge port. The impeller is a circular pump part that rotates to provide centrifugal force for propelling water in the circulation system. It spins on the end of the electric motor shaft and is the only moving part of a centrifugal pump.
The velocity (or speed) transferred to the water by the impeller is converted to pressure energy, otherwise known as total dynamic head (TDH). Two things make centrifugal pumps unique:
- They can provide high flow rates.
- Their flow rate varies considerably with changes in the TDH of the particular piping system. This allows the flow rate to be ‘throttled’ considerably with a simple valve placed into the discharge piping, without causing excessive pressure build up or the need for a pressure-relief valve.
However, throttling the flow rate of a centrifugal pump has certain limits, as it should not be operated below the minimum (safe) flow rate that is indicated by the pump manufacturer, or what is required for the given turnover rate. If this happens, it can cause excessive recirculation to occur inside the pump casing, resulting in the pump overheating and increasing wear and tear on internal seals and bearings. The ideal flow rate is the point at which efficiency of the pump maximizes energy use and reduces deterioration of the internal components.
Atmospheric pressure also affects the pump’s ability to operate. A self-priming pump will lose 10 percent of its ability to lift water for every 305 m (1000 ft) of elevation. For example, at 1534 m (5000 ft) a pump can lift water 1.5 m (5 ft), while at sea level a pump can lift water up to 3 m (10 ft). In other words, the atmospheric pressure at sea level is 6.6 kg (14.7 lbs), while at 1534 m (5000 ft) the pressure is 5.4 kg (12 lbs). This is important to remember because the higher the elevation, the more vacuum required in the system to make the pump operate properly.
Throttling centrifugal pumps with a discharge valve is not as energy-efficient as using a variable-frequency drive (VFD) to slow the pump/motor speed down, but it is much less expensive to install. To understand why many utilities are offering large incentives and rebates to those that switch from single-speed pumps to VSPs, it is important to understand how they differ.
Pump motor differences
Historically, pool pumps with induction motors, which only operate at one or two speeds, draw more energy than is necessary to circulate water and, in some cases, pump more water than necessary. These units must constantly operate at high speed to perform demanding jobs such as running a waterfall or pool cleaner. On the other hand, it takes far less power to filter the pool water—a difference single-speed pumps cannot address.
The programmability of a VSP is where these pumps differ. In fact, some have built-in, constant-flow software, which maximizes the advantages of these pumps, as it will automatically adjust its speed to deliver the required flow rate for each programmed task. For instance, to achieve the maximum laminar jet height of 2.1 m (7 ft) at a distance of 2.4 m (8 ft), a water supply of 37.8 litres per minute (lpm) (10 gallons per minute [gpm]) with 4.8 m (16 ft) of head (measured at the laminar) is required to produce a smooth 1.8-m (6-ft) arc of water. As the filter accumulates dirt, however, the pump will sense resistance in the circulation system and automatically ramp up its speed to continually provide the proper flow rate the water feature requires. With other pump types, the water feature will gradually throw a shorter arc of water as the filter gets dirtier.
VFD pumps can also be programmed to achieve turnover rates of exactly four hours, even if the filter is dirty. This allows for the reduction of motor speed, power, and energy use during periods when filters are clean, instead of sizing the pump to assume worst-case operating conditions.
No matter what type of pump is being used, however, slower speeds save energy, reduce noise levels, as well as wear and tear on other pool equipment the water circulates through.
How aquatic facilities can benefit from pump efficiency
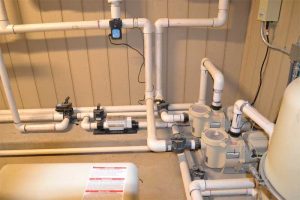
Some variable-speed pumps (VSPs) have built-in, constant-flow software, which automatically adjusts the pump’s speed to deliver the required flow rate for each programmed task.
With respect to commercial pools, a three-phase pump is a no-brainer as it can save an aquatic facility approximately 35 to 60 percent on its energy bills in comparison to using a one- or two-speed model.
Further, when combined with a VFD, it increases the pump’s efficiencies, as well as provides better energy savings. Even with a single-phase application, a VFD can be used with a three-phase pump to bring savings to those aquatic facilities as well.
Technological advancements in today’s pool equipment make it imperative for industry professionals to take the time to sit with facility managers to ensure they are achieving the water quality, parameter reporting, and cost controls necessary to keep their facilities operating efficiently.
With many municipal and YMCA-type pools struggling to keep their doors open, the integration of all components in the pump room is paramount to ensuring the lowest possible operating costs. This was the case for one such facility in Woodstock, Ont., with a 331,829-L (87,660-gal) pool built more than 35 years ago. Hollandia Pools and Spas, a commercial design/build and service company based in London, Ont., was called upon to design and renovate the equipment room.
“Having the opportunity to design the pump room for maximum efficiencies allowed us to not only upgrade the existing equipment but also enabled us to integrate additional technologies to improve the pool’s operating efficiencies and at the same time increase the facility’s cost savings,” says the company’s Richard Deakin.
A big part of the energy savings provided to this particular YMCA was the result of the installation of VFDs on the pumps.
“The facilities where we have installed these units typically see an annual savings of at least $10,000 in operating costs,” says Deakin. “The units are not free, but the return on investment (ROI) is normally less than three years, and some areas are even being given rebates from utility companies, making the payback period even shorter.”
Selecting the right pump
Proper pump selection (sizing) and optimal flow rates (as mentioned above), are additional ways to reduce energy costs. Affinity laws indicate the power demanded by a pump is proportional to the cube of the flow rate. For example, if the pump’s flow rate is doubled, then its power demand is increased by a factor of eight. Therefore, it is important to use the smallest pump that is capable of turning over the entire pool volume in an acceptable amount of time.
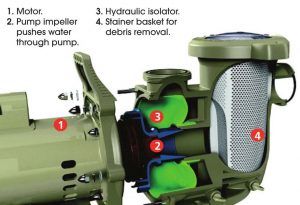
Variable-speed pump (VSP) cross section.
During the pump selection phase for an aquatic facility, the auxiliary features (e.g. spray pads, fountains, and waterfalls) should also be considered, as it is common for them to use the pool’s main pump. Some building codes, however, require the use of a multi-speed pump, or in some cases, a separate pump for each auxiliary pool load. Pumps for aquatic facilities are oversized by design, sometimes more than 20 to 40 percent bigger than they need to be. This is because many architects and engineers look at what is required, then pick the next size up to be sure the pump can handle the job.
Equipment costs versus energy savings
Even with the advantages explained, some homeowners and facility operators still find the cost of a VSP or VFD hard to justify. However, before ruling one out, the price of a new pump should be compared to the expense of doing nothing.
For example, an aquatic facility using a single-speed pump may have operational costs of up to $900 per year. After five years, the facility will have spent $4500 to operate the pump. However, comparable operational costs for a facility with a well-designed circulation system that uses a VSP or VFD may be as little as $200 per year. During the same five-year period, it would cost the facility less than a quarter the amount it would have spent using a single-speed pump. Cost savings will continue to multiply the longer the VSP or VFD is used. (Costs and savings will vary by region). The initial cost of a VSP or VFD can typically be recouped during the second year of operation, especially in pool facilities that operate year-round.
With the substantial energy-use rebates some local power companies offer, in conjunction with the savings in daily operational expenses, some end-users are getting back approximately 50 percent of the pump’s cost in less than a year.
This article was written by Mike Fowler and originally appeared on Pool & Spa Marketing [link].