Many indoor pool managers will inevitably face the challenge of replacing the dehumidification system at their facility. There are hundreds if not thousands of commercial aquatic facilities in North America. The majority of these indoor pools either surpass 10 years of age or use refrigerants that are being phased out or are banned, which accelerates their obsolescence. Upgrading these facilities to current industry standards will be difficult. Unfortunately for facility managers, the majority of these pools’ mechanical rooms were designed and built without much thought of replacing the dehumidifier. Thus, a majority of mechanical rooms have access doors that only pedestrians can walk through. Even double-door mechanical rooms cannot accommodate the removal of a small commercial dehumidifier.
Depending on how large the aquatic facility is, a dehumidifier system can range from 1.2 x 2.4 m (4 x 8 ft) to the size of a shipping container. To remove these units, the existing dehumidifier must be cut into several smaller sections to piecemeal them through the mechanical room doors. Once complete, the heating, ventilating, and air conditioning (HVAC) contractor faces a more skillful challenge—getting a new, similar-sized unit through the same access door(s).
This challenge will soon become reality for many because dehumidifiers manufactured and installed between 1980 and 2000 are now reaching the end of their lifecycle. In fact, systems installed as recent as 2009 could be using refrigerants that are being phased out as per the Montreal Protocol.
Do not replace, just supplant
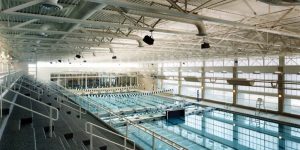
The 20-year-old dehumidification systems used at Adlai E. Stevenson High School’s 3716-m2 (40,000-sf) natatorium, required tens of thousands of dollars in annual maintenance and repair.
Manufacturers are well aware of this situation as they are now getting requests for replacement dehumidifiers with dimensions that will never fit through the equipment room access doors of an indoor pool requiring a retrofit.
To get around this impasse, alternative installation methods are now being used. One of the first of its kind was performed at Adlai E. Stevenson High School, in Lincolnwood, Ill. Instead of removing the school’s 4.5- x 2.7- x 2.4-m (15- x 9- x 8-ft) and 4.5- x 2.1- x 2.4-m (15- x 7- x 8-ft) heat recovery dehumidifier systems (circa 1995), the school had all new components installed piece-by-piece into the existing shells of each unit after gutting them.
Conceived by the school district’s long-time building automation and energy services contractor, this resolution circumvented $400,000 in construction costs to tear open a wall or roof for their removal, says Mark Michelini, CPA, assistant superintendent for business at School District 125. The natatorium’s retrofit also included a new scoreboard, pool surfacing, and energy-efficient lighting.
The 20-year-old dehumidification systems used for the school’s 3716-m2 (40,000-sf) natatorium, one of only four 100-m Olympic-size pools in the state, also required tens of thousands of dollars in annual maintenance and repair over the last few years.
The dehumidifier manufacturer commissioned for the project custom-built components for a 64- and 40-ton dehumidifier, including coils, piping inlet/outlet receptacles, and control packages that would fit inside the original manufacturer’s steel-shell configurations.
This installation technique, which may become a standard retrofit procedure, was also approved by the school’s on-site building services contractor, manufacturer’s representative, and architect consultant firm. As a result, the school district signed a performance contract to guarantee the dehumidifier replacement challenge would be solved at a specified payback and cost.
Rise to the challenge
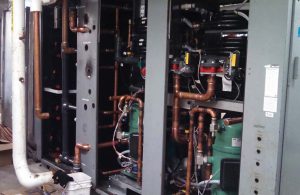
Instead of removing the heat recovery dehumidifier systems at Adlai E. Stevenson High School, the units were gutted and all new components were installed piece-by-piece into the existing shells.
Most of the challenge rested on the manufacturer, which sent factory production experts to the site to measure the shells, components, various piping connections, positions of inlets/outlets, and the 11.7- and 7.1-m3/s (25,000- and 15,000-cfm) blowers. The latter were retained and reconditioned to value-engineer project costs. Matching the evaporator coils was the most difficult challenge.
Factory engineers then designed the entire configuration and provided the installing contractor with 3-D, computer-modeled blueprints to simplify on-site assembly and installation. The new partially assembled internal component packages arrived as a compressor/refrigeration circuit skid, separate fully dipped enamel corrosion-resistant evaporator, reheat, and hot water coils, microprocessor controller/electrical control panels, and dry coolers to minimize on-site assembly.
“All dehumidifier manufacturers have a similar physical airflow sequence consisting of an evaporator coil, reheat coils, compressor module/refrigeration circuit and fans, but fitting equipment into another manufacturer’s configuration and making it easy for the contractor to install was a custom-engineering feat,” says Bruce Svec, a sales engineer with manufacturer’s rep Imbert Corp., who helped coordinate the project.
The new dehumidifier also includes modern technology that enhances the school district’s ambitious green mission. Instead of a conventional 100 percent refrigerant dehumidifier, two models were installed, which together substitute nearly 544 kg (1200 lbs) of the original systems’ refrigerant by using glycol, an environmentally friendly alternative. The glycol is supplied via polyvinyl chloride (PVC) piping to rooftop dry coolers 18 m (60 ft) away for heat rejection. The units also use a substantially reduced charge of approximately 181 kg (400 lbs)
of R-410A, an environmentally friendly refrigerant which does not have ozone-depleting chemicals such as chlorine.
According to Michelini, there is a noticeable difference between the old and new technology in terms of air comfort, especially in the 240-seat spectator section during swim meets.
Sustainability efforts payoff
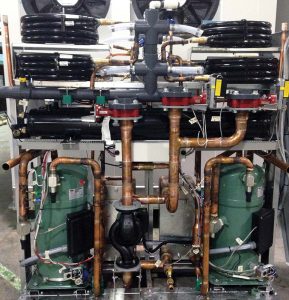
New, partially assembled internal component packages arrived as a compressor/refrigeration circuit skid to minimize on-site assembly.
The school’s ongoing progressive sustainability efforts, such as high-efficiency pumps, condensing boilers, and various lighting and plumbing upgrades, for example, have led to the district’s Leadership in Environmental and Energy Design (LEED®) Gold certification.
“Reducing refrigerant and chemical use in the school’s dehumidification system is part of our sustainability mission,” says Michelini.
Besides refrigerant reduction, the new dehumidifiers also save 15 to 20 percent more energy than their predecessors via scroll compressors, direct-drive fans, and other comparably higher efficiency components. Besides sustaining a 50 percent relative humidity, the units use energy recovery to heat the pool water to 26.6 C (80 F), as well as maintain indoor temperatures at 27.7 C (82 F).
Also lending to the project’s success was the pool did not need to be closed during the three-month retrofit. One unit operated continually while the other was installed. Thus, the pool, which hosts important state swimming events, remained operational during its typical 16-hour days.
It was suspected the original dehumidifiers may have unknowingly experienced slowly degrading inefficiencies in between routine annual service checkups. The new dehumidifiers will never run inefficiently because they are equipped with an onboard microprocessor and Ethernet connection that relays more than 100 operating parameters for review to the factory or the end-users authorized personnel or service contractor via smartphone or personal computer.
An operating inefficiency can be pinpointed and corrected the day it occurs, rather than discovered months later during a semi-annual service call. The operational data log history can be used by factory engineers to help local contractors troubleshoot and repair service issues.
Refrigerant leaks will close some natatoriums
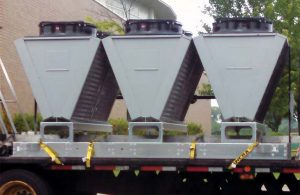
Internal component packages also comprised separate fully dipped enamel corrosion-resistant evaporator, reheat and hot water coils, microprocessor controller/electrical control panels, and dry coolers.
Michelini says the school could have postponed the dehumidifier retrofit another five years; however, the R-22 refrigerant-based units were leaking regularly, which increased maintenance costs. Since R-22’s chemical makeup includes chlorine, a major leak and total refrigerant loss of either unit would have damaged the environment and strained the school district’s budget. Further, replenishing a total charge of R-22 refrigerant would cost a minimum of $20,000, as its prices are increasing as the U.S. Environmental Protection Agency (EPA) continues to phase out hydrochlorofluorocarbons (HCFCs) until the complete ban in 2020.
The strategy of reducing potential environmentally damaging refrigerants also enhances the school district’s aggressive green mission, which typically includes annual carbon footprint reductions aimed at cutting energy use by three to five percent annually.
The R-22 debacle is prompting many indoor pool facility managers to replace their outdated dehumidifiers for fear of a catastrophic leak. All refrigeration coils, whether in a residential five-ton central air conditioner or an 80-ton commercial dehumidifier, will likely leak at least once in its lifecycle. Therefore, as R-22 prices increase due to dwindling supply and the fact the majority of dehumidifiers manufactured before 2006 likely use it, a total loss of refrigerant from a leak at medium to large natatoriums could cost upwards of $40,000 in replacement costs alone. Hopefully, for the commercial indoor pool operator, a total loss of a large unit will not bankrupt the center or force it to close temporarily until repair funds are secured.
This potential for leaks is driving many indoor pool operators to prematurely replace their R-22 dehumidifiers with modern units, which use 80 percent less refrigerant. The little refrigerant they do use (R-410A) is environmentally acceptable and significantly less expensive.
Another consideration for retiring older units prematurely is efficiency. Today’s technological advancements are more efficient than their predecessors 20 or even 10 years ago. The emergence of direct-drive fans versus belt-driven fans, electronically commutated motors, exhaust heat recovery, and other technology can be the deciding factor in retiring an older dehumidifier simply because the payback in energy savings can be substantial.
Going modular
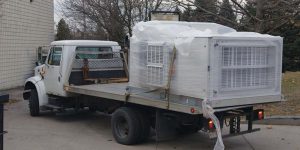
Two to four modular dehumidification systems can be individually wheeled through single- or double-pedestrian doors and then combined to equal the capacity of one large unit.
In addition to gutting existing dehumidifier shells that cannot be removed from mechanical rooms without the high cost of altering the building envelope, manufacturers have also developed modular units. These smaller systems fit through 813-mm (32-in.) doorways and can be installed in tandem. Two to four modular units can be individually wheeled through single- or double-pedestrian doors and then combined to equal the capacity of one large unit.
A case in point is the Cummer Park Community Centre in Toronto. The lifecycle of the 25-m pool’s dehumidifier was over; however, there was no way the manufacturer’s representative/contractor on the project was going to get a new dehumidifier, the same size as the existing system (4.8 x 2.4 x 2.4 m [16 x 8 x 8 ft]), through the mechanical room’s 1219-mm (48-in.) wide doorway. An original design called for two half-sized units with a remote exhaust fan and two separate heat recovery units. This would have made ductwork connections and controlling two separate units quite challenging.
Instead, the contractor installed two, 16-ton (2.3- x 1.5-m [7.5- x 5-ft]) modular units that could fit through 1117-mm (44-in.) access doors. The two units are stacked on top of each other and are designed for integration of heat recovery and exhaust fans, making for an easy installation and cost savings for the city. Typically, modular units stacked on top of each other equal a significantly smaller footprint than a conventional dehumidifier; however, for the Cummer Park project, energy-saving components that were previously remote from the original dehumidifier, such as exhaust air-energy recovery, were packaged inside the modular units, which accounted for a similar footprint.
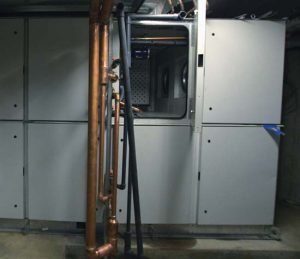
Typically, modular units stacked on top of each other require a significantly smaller footprint than a conventional dehumidifier; however, for the Cummer Park project in Toronto, energy-saving components were packaged inside the modular units, which accounted for a similar footprint.
Modular units are designed for this purpose and are easily and quickly piped and wired together once they have been wheeled into the mechanical room. Since they are separate units—each having its own compressor, coil, and supply air fan—they can operate together or independently in staged operation, which can add energy and redundancy benefits for the facility.
The staging ability modular units offer is particularly strategic for natatoriums with activities carrying varying capacities. A small swimming class comprising less than 10 bathers requires less dehumidifier capacity compared to dozens of people in an active public swim period or a six-hour-long swim meet with hundreds of participants and spectators. Natatoriums with one large system uses its full capacity compressor to handle any event, whereas two modular units could be staged down to operate just one smaller compressor during less occupied periods or even unoccupied nighttime settings.
Additionally, modular units offer redundancy. For example, a natatorium equipped with one large system would need to go without dehumidification—should the unit breakdown—until the repair is completed. Conversely, if one of two modular units breaks down at an aquatic facility, the remaining unit can still dehumidify the indoor environment to some degree.
Now anything is possible
Tight, inaccessible mechanical rooms have dealt today’s indoor pool facility manager a hand that might initially seem impossible to overcome when it is time to replace the dehumidification system. That said, a good look at the new techniques manufacturers have developed to override these setbacks deserve consideration versus the expensive approach of other construction-centric methods to accommodate the installation of a new dehumidifier into a small mechanical room.
This article was written by Ralph Kittler, P.Eng. and originally appeared on Pool & Spa Marketing [link].