Proper water balance in commercial pools and spas can be the difference between a safe, attractive facility and a disastrous one. Advances in chemical automation, disinfection methods, and better education on the problems associated with water chemistry have made the aquatic facility operator’s job easier when ensuring pool and spa water is safe for bathers.
Oxidation reduction potential (ORP)/pH controllers have been used since the mid-’70s; however, these systems were large and expensive. As a result, they were typically used primarily by municipalities and large aquatic facilities. Some of the greatest innovations were introduced in the early ’90s when microprocessor technology superseded analog equipment. The introduction of the two-pool controller with modem communications became an extremely powerful tool which allowed facility operators to monitor and control pool/spa water remotely.
In fact, remote communications has made it possible for facility operators to become proactive in pool/spa water management. Whenever water chemistry falls below the established threshold, the chemical controller is capable of sending a message to a facility operator’s mobile device, in addition to allowing him/her to log in to the controller, to diagnose and correct the problem before it becomes a health issue.
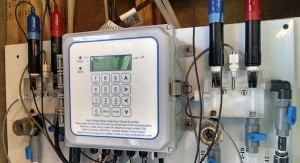
Chemical automation using direct connections from microprocessor-based programmable controllers to a wireless Internet database management system provides facility operators with real-time water chemistry data.
Chemical automation using direct connections from microprocessor-based programmable controllers to a wireless Internet database management system provides facility operators with real-time water chemistry data. Programmable chemical controllers have now become the reporting media, transferring information from the aquatic facility to a ‘readily accessible’ record of the water’s current and past status. Using this technology, facility operators can monitor and control the water’s chemical balance with more accuracy than in the past.
Despite the fact these devices are now commonplace in most aquatic facilities; many do not fully understand how they work. ORP is a qualitative measurement, not a quantitative measurement, and is affected by many factors, including the biggest variables in pool/spa water chemistry, such as pH, cyanuric acid (CNOH)3, and salt.
Health departments require a specific range of chemical residuals, which leads people to look at ORP and parts per million (ppm) charts to establish chlorine residuals mandated by local health authorities. This situation can be confusing for some facility operators because the water is often in compliance with ppm, pH, and cyanuric acid, but has unacceptably low ORP levels to effectively oxidize and sanitize the water. Conversely, there are also pools and spas that are well below the required ppm levels, but have exceptional water quality.
Oxidation reduction potential and parts per million
The misunderstanding between ORP and ppm has occurred since chemical controllers were first introduced to the aquatics industry. If properly understood, pools/spas can be run efficiently with an ORP controller. For many facility operators, water chemistry is a small part of their job, but health departments want pool/spa water to have a specific amount of sanitizer in ppm. As a result, chemical controller manufacturers have developed equipment with sensors capable of measuring sanitizers in ppm, or quantity of chlorine, to help eliminate this problem.
Most controllers will measure the levels of sanitizer and pH in a body of water. The three most popular sanitizer measurements, however, are: ORP, amperometric ppm, and colourimetric ppm. Understanding the basis of each measurement can assist facility operators in managing pool and/or spa water.
ORP
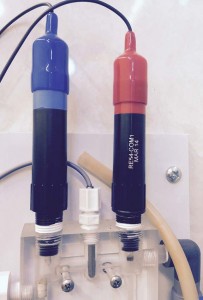
Standard oxidation reduction potential (ORP) and pH sensors used in a chemical controller.
ORP is a measurement of the oxidizing properties of the sanitizer present in a body of water. Most chemical controllers use a bypass mechanism that takes a small water sample from the circulation system, directing it into a small container that houses the chemical controller’s sensors. An ORP sensor comprises two electrodes, generally a platinum electrode in contact with the water, and a reference electrode inside an electrolyte chamber. A membrane separates the electrodes from the electrolyte solution. This membrane prevents the loss of the electrolyte solution and stops contaminants from entering the sensor housing. The output from the sensor is a voltage, typically expressed as millivolts.
ORP measures the waters’ ability to oxidize and is dependent on pH when the primary sanitizer is chlorine (Cl). Cyanuric acid levels can influence the readings taken by an ORP sensor, while salt systems can also affect ORP sensors and, in some cases, special metals must be used for the electrodes to prevent buildup on the sensor.
ORP is probably the most common and inexpensive method used by chemical controllers to measure sanitizer levels. This measurement, however, is the water’s ability to oxidize, not the actual amount of sanitizer. This is important to understand as it can be misleading for some inexperienced facility operators.
Some chemical controllers calculate the chlorine concentration based on ORP, pH, and temperature measurements. Therefore, it is important to remember the ORP sensor does not measure anything specific, and it will not differentiate between ozone and bromine.
Selective membrane ppm
The total amount of sanitizer in pool/spa water is measured in ppm. Like ORP, selective membrane ppm measurements are taken with a sensor that is housed in a small chamber located on a bypass from the main plumbing.
Selective membrane ppm provides direct readings of free chlorine in water. These are true readings, not indirect values derived from ORP. The ppm sensor is not affected by cyanuric acid and potassium monopersulfate (MPS), which assures constant readings of free chlorine at all times.
Colourimetric ppm
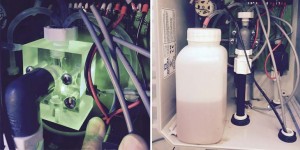
Colourimetric systems are some of the most accurate and expensive automated sanitizer measuring systems available. These units use reaction-based chemical indicators to detect the presence of a specified chemical.
This method also measures sanitizer levels in ppm; however, the process is much different. The term colourimetric is used to describe a measurement system where reaction-based chemical indicators are used to detect the presence of a specified chemical. The indicator reacts with the specified chemical and produces a visible colour change in the solution. The stronger the colour, the more compound is in the solution. A DPD (N,N Diethyl-1,4 phenylenediamine sulfate) test kit is an example of a colourimetric measuring device used in the aquatics industry.
Studies have shown there can be significant differences in readings when using these test kits due to differences in colour perception between individual users. However, this method can be quite accurate when the eye evaluating the test is automated. Essentially, a colourimetric system, which is a separate unit from the chemical controller, automates a manual water test. The chemical controller can be programmed to send a signal to the colourimetric unit to test chemical levels in the water at defined intervals, or periodically, throughout each day.
During the testing process, a chamber is filled with a water sample from the pool or spa and a beam of light is sent through the test chamber where it is detected on the other side to establish a base reading. Then, reagents are added and mixed with the sample before a beam of light is once again sent through the test chamber. These results are then measured against the base reading to determine the amount of sanitizer in the water.
Colourimetric systems are some of the most accurate and expensive automated sanitizer measuring systems available. The sensors used by these systems also require flushing the water sample to waste, which can amount to 7.5 to 11.3 L (2 to 3 gal) of water per day.
ppm
This is the easiest sanitizer measurement for end users to understand as the system is easy to set-up and maintain.
Primary disinfection and pH control
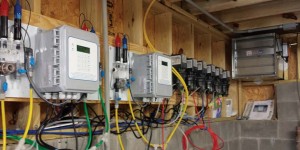
Remote communications has made it possible for facility operators to become proactive in pool/spa water maintenance management.
Primary disinfection using sodium hypochlorite (NaClO), calcium hypochlorite (Ca[ClO]2), bromine (Br), dichloroisocyanuric acid (C[O]NCl)2(C[O]NH), trichloroisocyanuric acid (C3Cl3N3O3), or chlorine generation (salt systems) have always been part of commercial pool and spa automation. However, chemical automation now goes beyond primary disinfection and pH control with methods for secondary disinfection, as recommended by the Centers for Disease Control and Prevention’s (CDC’s) Model Aquatic Health Code (MAHC).
Secondary disinfection support
More often than not, the industry is now seeing the need for a secondary disinfection system as a backup to the primary unit. As a result, today’s chemical controllers are now capable of automating, managing, and supporting the use of substitute sanitizing systems, which is mandatory for saltwater pools.
Enzymes and shock treatments
Some controllers can also be set-up to add enzymes and shock treatments. This treatment can be scheduled to start automatically at a specific time and date, when bathers are not in the pool. However, facility operators should note, non-chlorine shock will cause a temporary increase in ORP and a false DPD reading.
Choosing the best chemical controller
All of the above should be taken into account when selecting the type of measurement system for a chemical controller. The cost of this equipment is often a hurdle in the decision-making process; however, the needs of the facility should be first and foremost, and then balanced with any possible monetary limitations.
The initial expense of most chemical controllers can be justified by operational cost savings as well as the increased longevity of equipment and pool/spa surfaces. Facility operator’s must also keep in mind the type of chemical controller selected should reflect the other equipment used at the facility.
For example, ORP is affected by pH and cyanuric acid, while colourimetric ppm measurements are the least susceptible. ORP chemical controllers will require the lowest investment and will tell a facility operator how much sanitizer is available for use. On the other hand, selective membrane sensor measurements tell the facility operator how much sanitizer is in the water. Therefore, a chemical controller capable of measuring both can help identify and solve problems when combined chlorine is present in the water. Further, both systems require less maintenance. Colourimetric units require minimal power, but require reagents and, thus, use more water for testing.
Further, for outdoor pools using cyanuric acid, facility operators should note actual chlorine levels (ppm) will fluctuate when there is ORP control due to the variables affecting these types of automatic chemical controllers. This fluctuation will occur during sunrise and dusk due to the chlorine molecules associating and disassociating from the cyanuric acid. Ideally, a facility will have ORP and ppm control to ensure the proper sanitizer levels required by local health authorities remain constant, while also measuring the true water quality.
This article was written by Lance Fitzsimmons and originally appeared on Pool & Spa Marketing [link].